Non-Destructive Testing
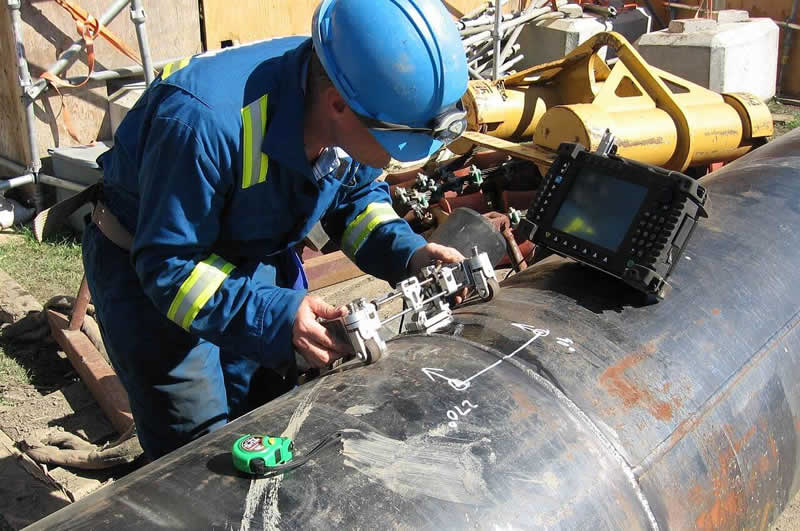
MB Iraq is well-equipped to handle nearly any reliability program requirement not matter the complexity or location. Non-destructive tests (NDT) will be executed by specialists according to international and national standards. These specialists are certified in accordance with EN473, ASNT-TC-1A and/or ISO9712.
MB is your one stop NDT service provider.
- Ultrasonic Testing (UT)
- Liquid Penetrant Inspection (LPI)
- Magnetic Particle Inspection (MPI)
- Radiography Testing X-ray (RT)
- Positive Material Identification (PMI)
Visual Testing (VT) also know as Visual Inspection, is an NDT method used extensively to evaluate the condition or the quality of an item. It is easily carried out, inexpensive and usually doesn’t require any special equipment. Visual Testing may be carried out by eye alone or can be enhanced by the use of optical systems such as magnifiers and microscopes.
A variety of equipment is available to the inspector including:
- mirrors,
- gauges,
- bore scopes,
- endoscopes,
- video / computer enhancement systems.
Visual Testing is a vital part of the in-service inspection and can identify such things as:
- fatigue cracks,
- creep failure,
- corrosion,
- erosion,
- abrasion,
- mechanical damage,
- wear and tear,
- distortion,
- poor workmanship.
It’s simple improving of VT reliability in specific applications. Although this is classified as surface method, we can distinguish between scratch and crack. Sensitivity increases, it means better resolution with more susceptible condition. Only open-to-surface defects can be detected, good cleaning is necessary. We reports just an indication; the real source stays uncertain (it is common feature of every method except VT). PT can be applied to smooth, clean surfaces. A productivity of PT lines is impressive: a batch of small object can be processed at once. Using fluorescent technique, the indication “shines” and is clearly visible. It’s the only method for e.g. chromium layer integrity investigation. A manual technique of cans (sprays) is very popular in the course of in-service inspections – detection of flaws and fatigue cracks
Ultrasonic Testing (UT) can be used for the detection of surface flaws and internal flaws in a range of materials typically steel, other metals and alloys.
This technique can also be used to determine the wall thickness of pipelines, tanks and vessels and also to monitor internal corrosion, all from the external surface.
Ultrasonic sound waves are typically introduced into the item under test via an ultrasonic source, coupling media and hand held probe. As this sound travels through the item, reflected echoes return from the back surface or internal discontinuities and generate a signal identified on the monitor for instant evaluation.
Echo time lags can be calculated to determine the thickness of the material and location / distance of any present flaws.
Ultrasonic testing can be used to test welds, castings and wrought products such as rolled plate and forgings.
Services on offer from MB :
- Portable Ultrasonic testing with the latest Sonatest digital sets.
- Electromagnetic acoustic transducer (EMAT) thickness surveys on fireside boiler tubes (no couplant or surface preparation required).
- Critical defect sizing, high temperature inspections, condition testing & paint / coating thickness checks.
- Comprehensive 24hr in-house and on-site service.
- Approved procedures for control checks.
- Approved procedures to specific industry standard.
- Inspectors fully qualified to PCN & SNT.
- Approved Method Statements, Risk Assessments and COSHH Assessments including confined space entry work.
It is suitable for inspection of metallic object. The equipment is similar to UT one in the mean of its complexity. The application is easier and handier, as there is not any couplant between our probe and the object surface. However, the inspected volume is limited to the surface and a near-to-surface layer.
A typical application is an investigation of manufactured tube integrity (a whole object is going through a coil) including welded tubes and their leak-tightness approval.
A specific application with inner coil is an inspection of heat exchanger tubing. The basic application is scanning of critical areas of operated structure for expected fatigue damage (0.2 mm crack can be reliably detected). We can also measure sheet thickness (up to several mm), cladding thickness (e.g. pure aluminium on aluminium alloy), protective coating (painting) thickness etc. A material sorting is also very popular; even a correct heat treatment can be witnessed.
Hardness Testing (HT) can be used to measure the hardness of a material to aid in material selection / acceptance and production testing.
The most common form of hardness test involves the Leeb Rebound principle where the hardness value is derived from the energy loss of a defined impact body after impacting on the surface of the component under test.
Generally the spherical test tip is fired within the impact device body at the test surface and rebounds faster from harder test samples than it does from soft ones.
The impact / rebound value can then be viewed instantly on the display screen and converted to all common hardness scales e.g. HV, HB, HRC, HRA, HS & Rm.
Services on offer from MB:
Portable hand held Proceq Equotip 3 Hardness Testers (Highly accurate ± 4HL).
Wide variety of impact devices and support rings to accommodate all shapes and sizes.
Comprehensive 24hr in-house and on-site service.
Approved procedures for control checks.
Fully trained Inspectors.
Approved Method Statements, Risk Assessments and confined space entry work.
Magnetic Particle Inspection “MPI” (also known as Magnetic Testing “MT”) is used for the detection of surface and near-surface flaws (such as cracks) in ferromagnetic materials e.g. steel and iron.
A magnetic field can be applied to the item under test by either direct magnetization or indirect magnetization.
Direct Magnetization is when an electric current is passed through the item under test and a subsequent magnetic field is formed within the material.
Indirect Magnetism is when no electric current is passed through the test object, but a magnetic field is applied from an outside source such as a 110v portable electromagnet or permanent magnet.
The presence of a surface or near surface discontinuity causes the magnetic flux to distort or leak. Fine magnetic particles (either dry or suspended in a carrier fluid) are applied to the surface of the item under test. These magnetic particles are attracted to any area of flux distortion or leakage thus creating a clear visible indication to the operator.
The more sensitive techniques of MPI utilize fluorescent magnetic particles which are viewed in a darkened area under a UV (black) light.
6000 Amp Magnaflux Bench Unit.
Fluorescent / Color Contrast techniques in-house and on-site.
Site services offering portable 110v coils, prods and electromagnets.
Comprehensive 24hr in-house and on-site service.
Approved procedures for control checks.
Approved procedures to specific industry standard.
Inspectors fully qualified to PCN & SNT.
Approved Method Statements, Risk Assessments and COSHH Assessments including confined space entry work.
GE Weldstar AUT, which our company utilizes, is the latest generation pipeline girth weld inspection system. This is an automated ultrasonic testing (AUT) solution that provides all functionalities required for the job, from setup to data archiving. Combining conventional and Phased Array ultrasonic, this advanced inspection tool provides the benefits of both techniques without compromise. GE Weld star’s unique modular design with ultrasonic electronics located on the scanner head and the simple umbilical that can be changed quickly provides huge benefits in terms of almost negligible interruption to work.
OTI AUT systems offer Inspection Integrity and Rapid Defect Detection through:
- Hybrid ultrasonic flexibility
- Highly versatile scanner design
- Industry-best resistant to electromagnetic interference
- Ultimate availability because of great reliability and ease of serviceability
- Reporting functions include statistical analysis, including trending, apart from regular reporting formats
The OmniScan family includes the innovative phased array and eddy current array test units, as well as the eddy current and conventional ultrasound modules.
The OmniScan MX ofers a high acquisition rate and powerful software features in a portable, modular mainframe to efficiently perform manual and automated inspections.
Typical Applications:
- Girth Weld Inspection
- Pressure Vessel Weld Inspection
- Scribe Marks Inspection with No Paint Removal
- Aircraft Fuselage Inspection
Imagine being able to see the damage happening to your equipment from extremely minute wear particles and debris. Oil analysis is a preventive maintenance tool that uncovers fixable problems before they become catastrophic failures. For you, it means less unscheduled downtime and increased equipment reliability, productivity and profitability. Oil analysis with MB can:
- Extend oil drain interval
- Extend equipment life
- Identify problems before equipment failure
Radiographic Testing (RT) can be used for the detection of hidden flaws in solid objects and requires either x-rays or gamma rays. One of these sources of ionising radiation is positioned on one side of the item to be inspected and a photographic film is placed in close proximity on the other side. The radiation is partly absorbed during transmission and differences in material thickness or absorption qualities are recorded on the film giving a full size image showing internal detail.
X-ray radiography is generated electrically by means of a high voltage x-ray tube. Gamma rays are produced by the natural disintegration on nuclei in a radioactive isotope. The main benefit of radiography is that it provides a non-destructive method of detecting hidden flaws and provides a permanent record in the form of a radiograph.
Services on offer from MB:
- 4 meter x 4 meter radiographic exposure bay.
- X-ray cabinet with Phillips 200kv set (for smaller items).
- 300kv directional x-ray set.
- Tech-ops 660 / 680 containers, selenium 75, iridium 192 and cobalt 60.
- Portable darkrooms’ for fast results on-site.
- Comprehensive 24hr in-house and on-site service.
- Approved procedures for control checks.
- Approved procedures to specific industry standard.
- Inspectors fully qualified to PCN & SNT.
- Approved Method Statements, Risk Assessments and COSHH Assessments including confined space entry.
Positive Material Identification (PMI) enables a components material grade / alloy composition to be found based on its elemental composition.
Many companies / industries have implemented stringent material identification procedures, as a result of a series of accidents in the past, resulting from material mix ups.
Positive material identification is now considered an integral part of process safety management across many industries and at Venture our skilled inspectors use the latest-ray fluorescence (XRF) analyzers for fast accurate results.
Services on offer from MB :
- Portable hand held Niton XRF Analyzers.
- Spectrographic Analysis.
- Identification / sorting of scrap metal for recycling.
- Comprehensive 24hr in-house and on-site service.
- Approved procedures for control checks.
- Fully trained Inspectors.
- Approved Method Statements, Risk Assessments and confined space entry work.
Dye Penetrant Inspection “DPI” (also known as Penetrant Testing “PT” or Liquid Penetrant Inspection “LPI”) is used for the detection of surface breaking flaws in all non-porous ferrous and non-ferrous materials of any size such as metals, plastics and ceramics.
Typical applications would be forged, cast or welded products which are prone to cracking and other surface flaws, or when Magnetic Particle Inspection is not practical for reasons such as material type or complex geometry.
A visible or fluorescent dye (either solvent or water based) can be applied to the surface of the item under test in several different ways such as spraying, brushing, dipping or immersion of the component into the dye.
During the penetration time (dwell time), the dye penetrates any surface breaking flaws through “capillary action”. Once the dwell time has been reached the excess dye is removed from the surface of the item under test leaving no dye visible to the naked eye. A developing agent is then applied which draws the dye out of any surface breaking flaws through reverse “capillary action” and clearly reveals this area to the operator.
Services on offer from MB :
- Fluorescent penetrant line for small and medium sized components.
- Fluorescent penetrant system for larger components.
- Site services offering colour contrast and fluorescent techniques.
- Portable quick assembly tents of various sizes for on-site fluorescent penetrant inspection.
- Comprehensive 24hr in-house and on-site service.
- Approved procedures for control checks.
- Approved procedures to specific industry standard.
- Inspectors fully qualified to PCN & SNT.
- Approved Method Statements, Risk Assessments and COSHH Assessments including confined space entry work.
Fun Facts
We Are The Leader In The Industry
0
Projects
0
Clients
0
Members
0
Awards
Other Services
Engineering
After the conception design phase and feasibility studies a project enters the engineer phase …
Construction
MB has built its reputation on the safety, quality and schedule performance we bring to our projects.
Testing and Commissioning
MB Iraq envisions consistently exceeding industry standards in Testing and Commissioning by use of new methodologies and technologies.
Supply Chain Management
MB is a player that sources competitively worldwide and can provide support to clients …